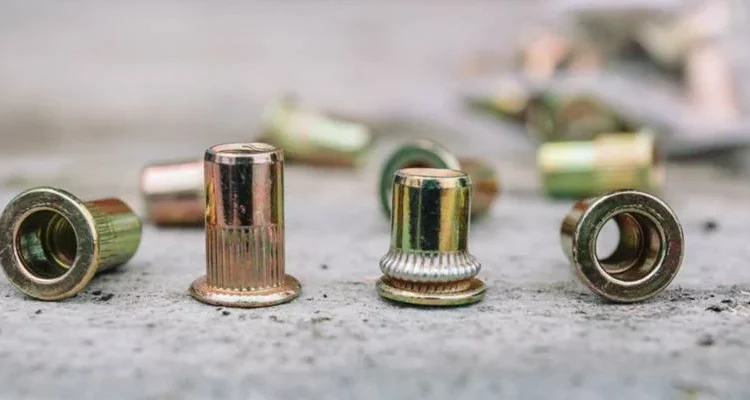
6 Types Of Rivets And When To Use Them
Solid rivets are ideal for construction and aerospace due to their durability. Blind and drive rivets offer easy installation in inaccessible and wooden areas, respectively, while tubular, split, and flush rivets cater to aesthetic, repair, and aerodynamic needs
Solid Rivets
Solid rivets are basic but one of the most reliable types primarily intended for application in those places where it is necessary to join two metals permanently. They are actively used in construction, especially bridge building, and aircraft production because they are considered to be one of the strongest items. Usually, the chosen rivet includes a solid shaft with a head and a tail that should be deformed with a hammer or another special device to keep any material fixed.
Application in Heavy-Duty Construction
These particular types of construction elements are used in heavy-duty construction as being able to accept as much load as is required. They provide better shear and tensile strength, which is essential for buildings and other objects of both regular and non-regular usage, exposed to various dynamic forces, vibration, shock load, and many other impacts. For instance, steel solid rivets varying in size ranging between 1/4” to 1” in diameter are frequently used in bridge and skyscraper building.
Installation Techniques
Typically, the experts’ assistance is required to install the discussed type of rivets. There are two important parties in such a process: one person holds a hefty bucking bar against the rivet’s tail; and the second one deforms the head by hitting it with a hammer or another heavier piece or uses a special air hammer or another tool. As well as the previous linking item, the discussed construction element expands and fills a hole, creating reliable and tight fixation. The only distinction is that it is applied in the cases where the possibility of welding is unavailable or the usage of a relatively weaker element is never an option.
Material Compatibility and Selection
Regardless of the type of applied material, it is crucial to “choose a rivet that will not corrode, so it does not combine the two materials”. The most common materials are aluminum, steel, and copper. The lightweight quality, as well as the ability to withstand any water corrosion, makes aluminum solid rivets a good choice for aerospace. In its turn, steel, being one of the firmest materials to melt, is considered to be excellent for different types of construction and industrial items. Copper solid rivets escape the influence of water corrosion and are often used in marine environments.
Advantages over Other Fasteners
Solid rivets tend to effectively replace welds in different constructions due to the significant cost reduction while the reliability of the final construction is completely equal to that of welded multiple parts. Furthermore, they are not applied on both sides, which is the case with bolts. As a consequence, the lines of the final result look much better without any additional welding work. As well, having no moving parts, solid rivets cannot accidentally loosen and be detached. That is why they are an excellent choice for any construction exposed to vibration or, for instance, temperature decreasing and increasing.
Maintenance and Inspection
One of the keys to a perfect solid rivet installation is regular maintenance mostly in the form of frequent and thorough inspections. The last ones are remarkably simple and require only checking the planted rivet for a failure and keeping it in a tight condition. The joint should not be watched as something to be oiled. However, in aircraft overhaul, where correctly dismantling the construction does not take long and is performed on the ground, the staff is careful about “varying types of corrosion between some materials”. Therefore, even a singly-loosened rivet can become the first sign of coming structural failure and should be checked.
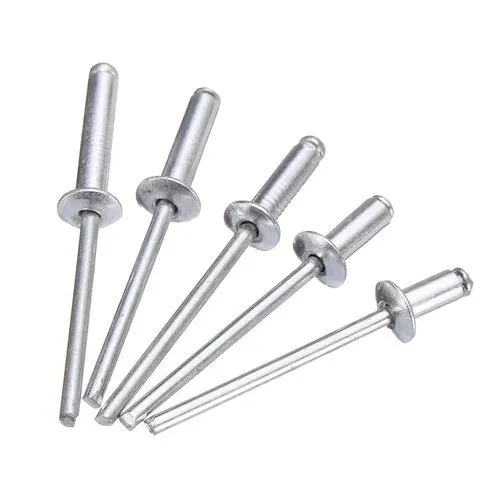
Pop Rivets, Size
Blind Rivets
Blind rivets, also known as pop rivets, are fasteners used with projects that require the joint to be accessible only from one side. They’re especially popular in industries like automotive repair and electronic assemblies where the rivet is not accessible once the job is completed. Blind rivets work well with a wide range of materials, including metals, plastics, and composites, providing excellent versatility in the manufacturing and repair of items that cannot be disturbed on both sides.
Applications
Blind rivets provide a unique advantage in the assembly of panels and trim in automotive construction. These fasteners support material thicknesses from 0.062 inches to 0.625 inches. The rivet itself consists of a smooth body that slides through the hole and expands to hold the materials securely. The installation process is quick and creates a safe, high-integrity fastener.
The Installation Process
Typically, the blind rivet is installed with the help of a rivet gun that pulls a mandrel through the body of the rivet. The mandrel forces the body to expand, giving the rivet a tight fit between the two materials that need to be fastened together. When the rivet is fully expanded, it breaks off and is collected in the handle of the rivet gun. This simple and quick process allows for fast and efficient installation. The speed of the process and the permanence of the joint which results, make these rivets a great choice for high-integrity applications, such as airframe construction.
Selection
The selection of a suitable blind rivet is determined mainly by the thickness of the materials and the mechanical load that the joint will experience. Aluminum rivets are the most common variety as this metal offers excellent strength-to-weight ratio and is virtually impervious to corrosion. Aluminum rivets are found in many automotive and aerospace applications. In environments where greater strength is required, and high corrosion-resistance is beneficial, the selection includes rivets made of stainless steel.
Advantages Over Solid Rivets
The main advantage of these rivets is the tremendous simplification of the assembly process. By allowing the use of only one side of the rivet, these fasteners outstrip heretofore common installation methods used with solid rivets. Being able to eliminate the need for two sides of the assembly to provide rivet access creates a greater overall speed in production lines all over the world. The disadvantage of the increased access requirement is born out with these rivets, and a linear decrease in labor costs may be observed.
Drive Rivets
Drive rivets represent a special category of fasteners, which are designed by the shape and a way of attachment to simplify the process of fastening. They are perfectly used in wood products and in the production of plastics where the pre-installation preparatory works are minimal or not required at all. Thanks to a simple design and the ability to be applied quickly, the present type of hardware provides significant benefits as far as the speed of the work is in question.
Usage in Furniture and Minor Construction
Drive rivets are widely used in the furniture industry where plenty of elements must be attached quickly to one another. The given device-type fixtures are also employed for light construction where the handiness of application makes the process many times faster. For instance, in the process of cabinetry, fixing of the elements and assembling, the specialist commonly chooses the solid drive rivets of the 1/8 inch to 1/4 inch diameter. These fasteners can be attached with a hammer, and no other instruments are needed for the process.
Technique of Installation
The technique of drive rivets installation is simple. The user must have a rivet and a hammer. The device is put in a hole of prespecified size, which is less than the rivet’s diameter. After this, the rivet is driven into the hole by means of the hammer in several strokes. The rest of the rivet begins to split and expand, and shaped as a tail, the device fixes the spacer in the material.
Options for the Selection
When choosing between the several varieties of drive rivets, one should take into consideration the strength of the material and the thickness of the object, so that the hardware could ensure necessary preservation of the workpiece. The rivets can be found in the materials of aluminum, steel, and nylon. The first type of the fastener is convenient for indoor because of its lightness and resistance to corrosion. Steel rivets are stronger than the aluminum ones and can be used outdoors. The present devices are designed for the fixing of the thick workpieces.
Benefits of Application in Production
Drive rivets have a number of advantages in comparison with classical means of fasteners. The main advantage is that they are attached on reasonable workpieces with a single stroke. No auxiliary instrument or space behind an aimed surface is required. The footage will look neat, no rivet head or tail will be observed, as there is nothing protruding from the gap.
Tubular Rivets
Tubular rivets can be identified by their hollow structure, which does not only make them lighter but also allows them to be used in applications where visual aspects are of great importance. They are typically used in the assembly of leather goods, textiles, and light metals to form clean and neat appearances. The employment of tubular rivets is quite common in the fashion industry, for example, to take different elements that adorn clothes, belts, and accessories. Besides, they are widely used to join plastics in the assembly of consumer electronics, where a tubular rivet provides the necessary neatly finished look when installing plastic parts.
Applications in the Fashion Industry
In the fashion industry, tubular rivets are used to connect various decorative elements to clothes, belts, and other accessories. Besides, consumer electronics frequently feature plastics, which need to be joined in order to form different electronic products. Tubular rivets can be used in this case to join different elements of plastic as the metal, which permits the plastic to create a clean and smooth appearance after being installed. Tubular rivets used for this purpose are typically between 1/16 inch and 1/8 inch in size, which is enough for plastics not subjected to mechanical loads to be assembled with the help of a tubular rivet.
How to Install Tubular Rivets
Installing tubular rivets requires a setting tool, which is used to flare the tubular rivet’s tail in the material it is attached to. It balances its head by forming a neat and round finish that is pushed into the material to prevent it from moving out. The process of installation is quite simple and can be completed with minimal effort. It includes piercing a pre-punched hole with a rivet and using the installation tool to press or roll the edging of the tubular part to flare them out and join these parts together.
Selecting the Appropriate Tubular Rivet
Selecting the appropriate tubular rivet requires taking a number of factors into account. In particular, both material and size should be assessed properly. Tubular rivets can be made of various materials, with the most commonly used being aluminum, brass, copper, and others. Aluminum is the primary choice for the majority of applications due to its light weight and resistance to corrosion, which allow it to be used both indoors and outdoors. Brass and copper are also used to assemble plastic parts for consumer electronics where tubular rivets are used in highly visible areas. Moreover, the appearance of the tubular rivet is crucial for them to be aesthetically pleasing and fitting the given purpose. Overall, tubular rivets can be exceptionally useful in applications where neat installation is of the essence since they allow for simple and rapid installation that does not cause damage to the attached materials. It may be particularly valuable in applications where the appearance of the fastener matters just as much as its fastening qualities.
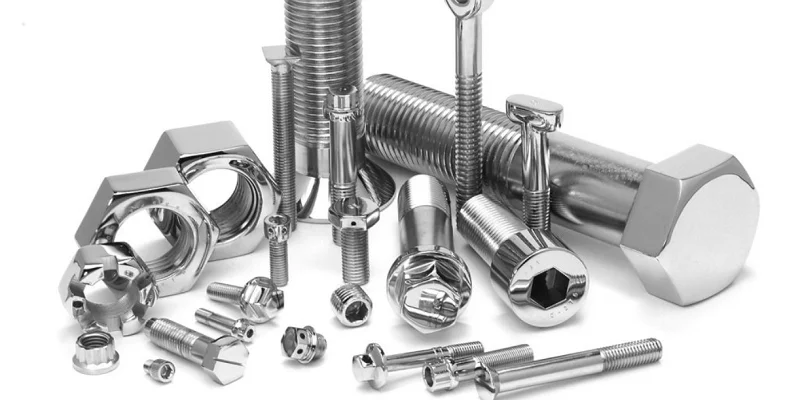
Types of Fasteners and Their Application – WayKen
Open Rivets
Open rivets, or open–end rivets, are widely used in manufacturing and construction to create strong bonds with visible access to the back side of the assembly. They are designed as a tubular shape with one end flared out, creating a button or flower which prevents an object from pushing through the hole. Open rivets can be applied in multiple industries due to the construction’s reliability and performance in specific settings.
Applications in Various Industries
The rivets are applicable across multiple industries to join metals, plastics, and other materials. They are typically used in automotive, aerospace, and other manufacturing areas where the joint’s strength is of concern and the finish is not essential. In automotive, open rivets are often used to connect body panels and frames. The installation does not require special skills as the two pieces can be put together and the tool can be used to flare the rivet. The typical sizes of the open rivets range from 1/8 inches to 1/4 inches in diameter, which are easily applied in a manufacturing setting with the help of a pneumatic riveter.
Installation Technique
Open rivets come in a tubular shape and are applied in pre-drilled holes. During installation, a tool is used on one side to pull the mandrel through the rivet on the other side. The open end is then flared onto the mandrel, creating a round and tight end between the two materials. The installation requires an operator to pull the mandrel, ensuring a strong and mechanically resistant connection for both light and heavy applications. In comparison with closed rivets, it is harder to deform the hollow tubular construction and hammer it in the tight space between the materials, even with the help of special riveting pliers.
Choosing the Right Open Rivet
Choosing the right rivet requires understanding the thickness of the materials and the load required to keep them together. It is also vital to consider the application where the rivets will be used to choose the most applicable material. Aluminum rivets are light at the expense of strength, while stainless steel or iron are strong and long-lasting but are harder to work with. It is cheaper and quicker to install the open instead of closed rivets as they require less mechanical force applied at the opening time. The end of open rivets is not closed, and engineers have a visual confirmation that the connection is strong enough for the application.
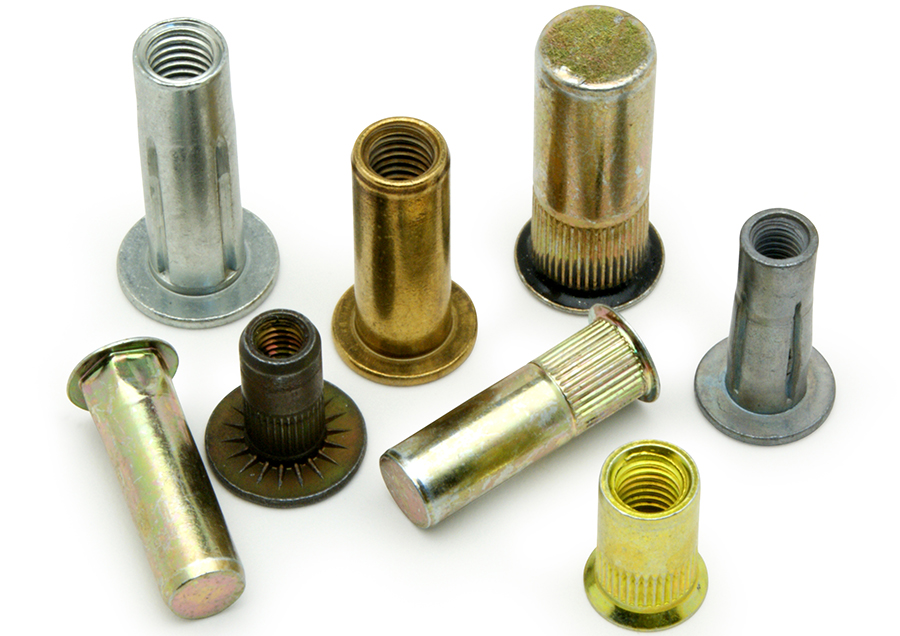
SONY DSC
Flat Head Rivets
Flat head rivets are a type of rivets that are used for tasks when it is particularly important for the rivets to be flat with the surface. They are widely used for both practical and aesthetic applications, as many aircraft and cars require flat head rivets to maintain the smooth and aesthetically pleasing design. They can serve practical uses, as the flat design can be useful for aerodynamics, and those applications make heavy use of such rivets.
Use in Aerospace
One area where these rivets are used is aerospace, where the flat shape reduces air resistance and ensures that the surface is not interrupted by additional components of an otherwise riveted construction. Smoothness of the design can be vital in minimizing even the slightest resistance to air currents, therefore, using flat head rivets across the body of the aircraft could be beneficial from a functional standpoint. Moreover, the design also offers an unobtrusive look, making the plane or rocket look more attractive.
Use in Automotive
Flat head rivets can be seen in the automotive industry, especially on visible metal parts, creating a consistent and flat design of hoods and other metal parts. The flat design of a rivet ensures that they “sit” flush with the other surfaces, in effect becoming as invisible as possible. This improves not only the functionality of the manufacturing process but the quality of the end product as well, particularly for consumers interested in streamlined or flat designs.
Installation
Flat head rivets are installed in a manner similar to other types of rivets though even more precise as their position in relation to the surface is especially important. Hole, somewhat smaller than the rivet, is drilled into the surface, and the rivet and then the shank are deformed at the other side by means of a tool. The shank does not protrude at any time, and the rivet is held firmly in place, entirely flush with the surface.