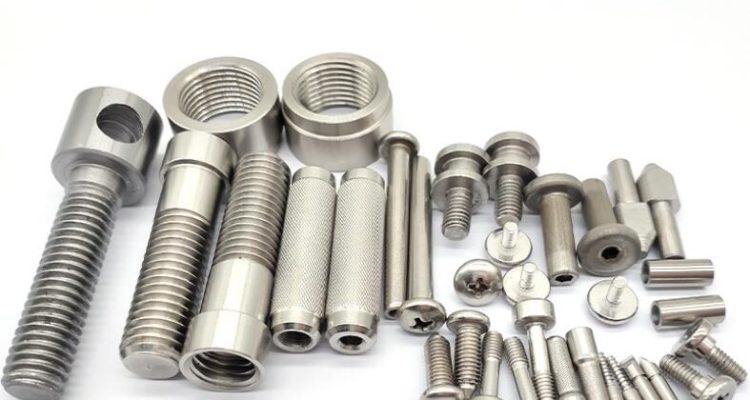
How to ensure quality when choosing a custom fastener provider
Ensure provider quality by vetting ISO 9001 certification, reviewing material samples, confirming custom capabilities, and assessing on-time delivery and customer satisfaction guarantees.
Identifying High-Quality Custom Fastener Manufacturers
Experience and knowledge
A search of a high-quality custom fastener manufacturer implies assessing experience and knowledge. This is likely to involve searching for a company that has a record of producing durable and reliable fasteners for a variety of applications within which customers apply the product. The experience or knowledge somewhat reflects the ability of a manufacturer to effectively conceptualize and then deliver the product according to requirements. Apart from experience, the staff members of an engineering team and their knowledge and capabilities in fasteners and hardware in general are also factors. A manufacturer that invests in understanding properties of different materials, types of fastener making, finishes, plating, heat treatments, mechanical properties, and industry application standards may have a better-developed ability to deliver custom fasteners according to expectations and requirements . Thus, any potential customer should ensure that they evaluate demonstrating experience and the extent of the customer’s knowledge and prototyping to develop high-quality custom fasteners.
Broad assortment of fasteners
Moreover, evaluating a broad assortment of fasteners’ types and sizes is essential. Indeed, it is unlikely that a customer will benefit from a manufacturer that specializes in a limited range of sizes and types. Instead, the variety reflects flexibility and the range of possibilities, including size, material, and type configurations needed for potential application. By evaluating a broad assortment of fasteners, a customer evaluates the ease of customization without compromising quality and other properties. In addition, a manufacturer specializing in a broad assortment also invests more funds into research and development and would be more likely to have stronger prototyping skills and facilities . Finally, prototyping capabilities is another factor that determines the quality and reliability of the custom-made fastener. A manufacturer with strong prototyping capabilities can create a prototype and gain customer insight into features of the final product and adjust.
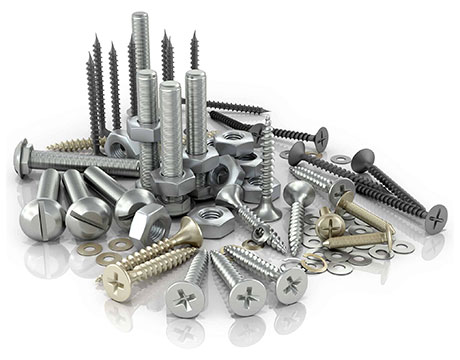
Industrial Fasteners & Fixings
Evaluating Technical Capabilities
Evaluate Manufacturer’s Manufacturing Facilities
When checking custom fastener manufacturers, it is crucial to evaluate the technical capabilities of their manufacturing facilities. One should look for fastener manufacturers who invest in state-of-the-art equipment and technology to ensure precision, speed, and consistency in the manufacturing process. Modern manufacturing facilities tend to employ the use of advanced CNC machines, robotic automation, and use of computers to control the quality of fasteners produced. These capabilities enable manufacturers to maintain tight tolerance, high production speed, and superior quality control. Custom fasteners produced in such facilities can be programmed to match even the most demanding specifications and performance requirements.
Safety and Material Quality
Safety and material quality are also paramount issues when selecting fasteners to be used for critical applications. A suitable manufacturer should ensure that safety is a priority for them and that a strict application of quality standards is maintained. The use of only the best materials source from reputable suppliers should be mandatory. Most high-performance materials such as stainless steel, titanium, or high alloy steel are far easier to source than lower grades materials. The best materials assure that fasteners produced are both strong and corrosion-resistant. Manufacturers should also ensure that they have measurements of tensile strength, resistance, and other useful quality specifications in place as well as perform testing such as hardness testing to ensure the products are of superior quality.
Industry-Specific Fasteners
Fasteners are used across many different industries for many different purposes. As a result, it is incumbent on manufacturers to produce industry-specific options in order to best cater to the needs of all sectors. For example, aerospace uses fasteners made from titanium while automotive uses fasteners made from high-quality stainless steel banning . Both fasteners have the best properties suited for the specific industry requirements. As such, partnering with manufacturers that have industry-specific fasteners ensures compatibility, reliability, and specific standards are met for industry fasteners, whether serving the aerospace, automotive, construction, or even marine industries.
Ensuring Compliance and Certification
The Importance of Meeting Industry Standards
Meeting industry standards is highly important to ensure that the custom fasteners are safe, reliable, and high-performing. Various industry standards provided by organizations such as ASTM International or the International Organization for Standardization specify the requirements and standards of different types of fasteners and their application. These standards are set to create products whose quality meets at least the minimal criteria to ensure compatibility and intercambiabilyty with other components and systems. Moreover, meeting established standards ensures that custom fasteners are safe to use and their performance is within the allowed range. Additionally, meeting the standards ensures that the fasteners have undergone testing and validation process and are in line with the requirements of customers and regulatory authorities.
Certifications as Indicators of Trust
Certifications are the most important indicators of trust when it comes to custom fasteners, as they attest to the commitment of the manufacturer to providing high-quality products and complying with the relavant standards. Whеn selecting a manufacturer for custom fasteners, users should always consider the fact whether the manufacturer holds necessary certifications and accreditations. Some of the common certifications include ISO 9001 Quality management systems and AS9100 aerospace quality management systems, which ensure that the manufacturer has established a process approach and implemented effective quality management system. There are also special industry requirements, such as Nadcap for aerospace manufacturing or IATF 16949 automotive quality management systems, which ensure that the manufacturer is proficient in the specific area. Opting for a certified manufacturer ensures that custom fasteners are in line with the stringent quality requirements and in compliance with the law, reducing the risk for the users.
Prioritizing Customer Satisfaction
Customer Service Excellence
Customer service excellence is one of the essential factors that ensure customer satisfaction throughout the entire purchasing process. It is characterized by responsive and timely service offered by knowledgeable and supportive representatives who provide personalized attention to any inquiries, concerns, or requests. The usage of phone, email, or live chat allows customers to contact the manufacturer with ease, and the manufacturers’ representatives can answer any questions and concerns that the customer might have, from customization and pricing to the shipping and tracking of the order. Thus, manufacturers can ensure high levels of customer satisfaction and promote the establishment of trusting relationships with their clients.
Customization and Responsiveness
Customers are satisfied with customization options regarding the materials, size, finish or packaging offered by the manufacturer. Companies that employ these options receive higher approval rates among their customers. Being responsive to the most urgent needs of the customer, such as a request to deliver the order earlier, is also considered a significant product satisfaction attribute. The importance of this factor is determined by the ability of customers and manufacturers to adjust to changing situations and requirements of the market and establish relationships that benefit all the involved parties. Thus, customer satisfaction is dependent on the ability of the manufacturer to adapt to the requirements of the customer and the market.
After-Sale Support and Services
After-sale support and services include the provision of both products and services that are associated with it. They can include the availability of technical support after the warranty period, assistance with coverage under the existing warranty, and assistance with warranty repair, including all necessary paperwork, shipping or inspections. All these options are essential for the build-up of customer satisfaction, as well as the decrease of returns. The success of the business is also impacted positively through the acquisition of customer feedback that can be used both for product and service improvement, allowing open communication with the client.
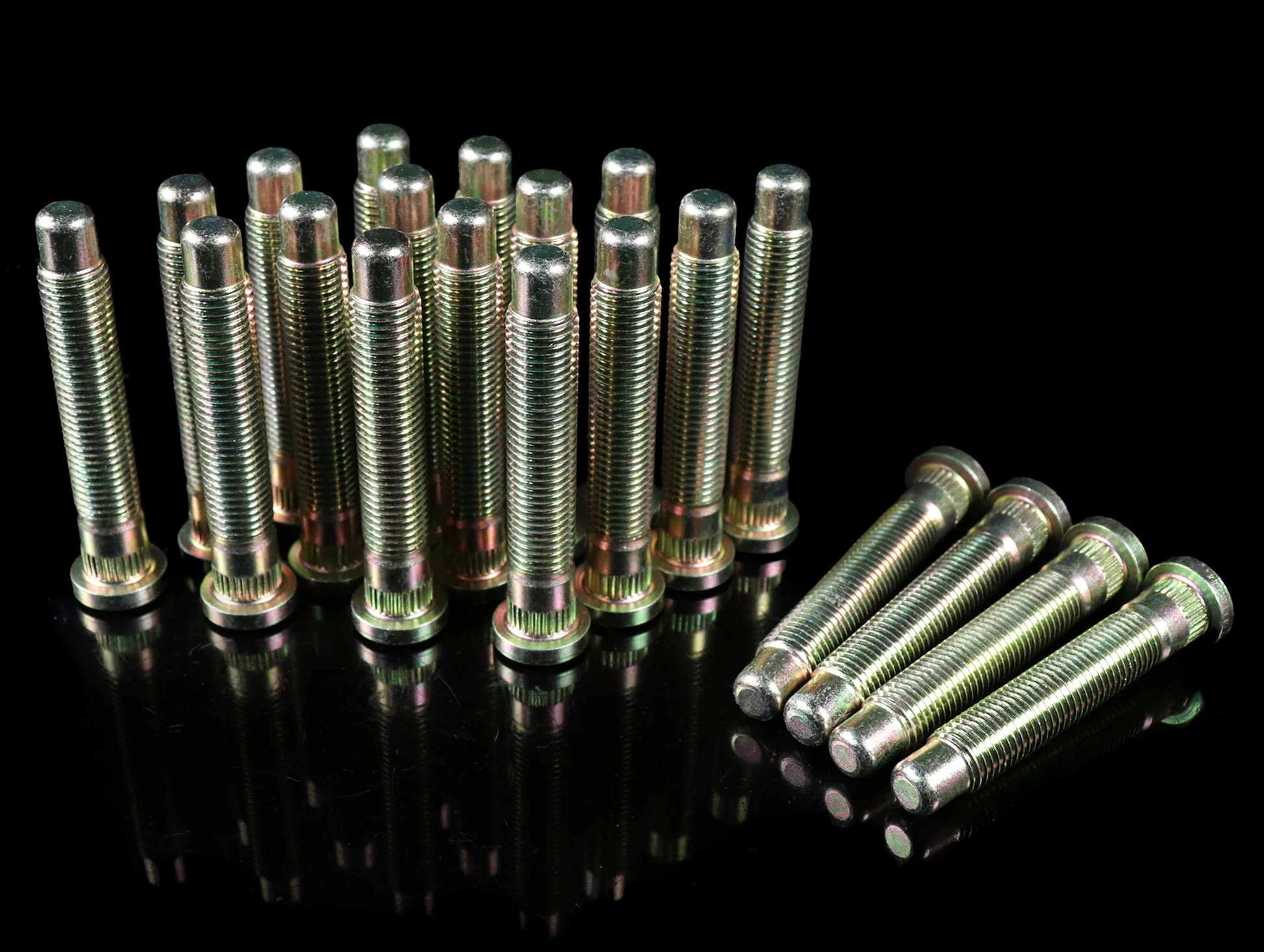
Hardrace Extended Wheel
Finalizing Your Fastener Supplier Choice
Pricing and quality comparison
Finalizing your fastener supplier choice demands a close comparison of pricing and quality before making a decision. Even though competitive pricing is critical to ensure optimal cost management, it should not undermine the importance of quality. When analyzing quotes offered by different suppliers, pay close attention to the competitiveness of the pricing and the quality of the provided fasteners . Although high-quality fasteners might require a slightly higher investment at the beginning, they will save you money in the long run by reducing expenses spent on maintenance, replacement, and downtime. As such, it is advisable to choose a supplier offering the most balanced and optimal combination of affordability and quality to ensure the greatest return on your investment.
The importance of the variety of products offered
The variety of products offered is crucial to ensuring that the needs of customers in a multitude of industries and applications are met. A supplier, in this case, should offer an exhaustive range of different types of fasteners, sizes, materials, and configurations. Some of the best suppliers offer both standard and custom fasteners to cater to the needs of every customer. Standard well-known fasteners can be easily ordered off-the-shelf, while sometimes rarer and highly specialized products might be required to meet particular requirements. Furthermore, a supplier’s level of the variety of products offered indicates a high level of commitment to different industries and proficiency in keeping abreast of the evolution of the market.
The evaluation of the competence of customer service
Finally, you should also consider the competence of a supplier’s customer service team as one of the final factors in your decision regarding your fastener supplier. Customer service should be highly knowledgeable and competent in response to all the questions you might have from the initial inquiry to post-sales support. Consider the responsiveness and professionalism of the communication with the customer service team and evaluate if they are accessible and communicate well . Moreover, the ability of the customer service agents to go the extra mile for you can also be the determining factor in your decision to choose a supplier with competent customer service and develop a lasting partnership.