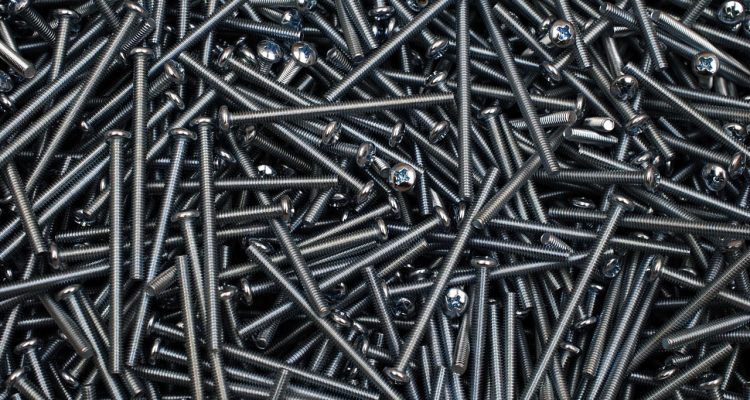
How to get custom screws made
Seek reputable manufacturers for custom screws based on specific dimensions and materials. Collaborate closely for precise specifications.
Table of Contents
ToggleUnderstanding Screw Types and Manufacturing
Learn different types of screws, such as different types of wood screws, machine screws, and sheet metal screws. These are used for specific purposes, with differences in the pitch of the thread, the shape and style of the head, and the type of metal or material. Learn about exploring manufacturing processes for producing custom screws, such as machining, cold heading, and thread rolling.
Material selection
This is a guide on the types of materials that can be used to manufacture custom-made screws. Learn about the application of different materials such as stainless steel, aluminum, brass, and titanium with different properties, including corrosion resistance, strength, and electrical and thermal conductivity. Lead in the selection of the material that is most suitable for different conditions and purposes. This helps in customization according to the requirements of specific applications, including industrial, high-precision, or small-scale equipment. Learn about the creation and specification calculation of the product to ensure the best choice.
Screw specification
Know the specifications of different types of screws, including the specification range and extent of customization. Important specifications include thread pitch, diameter, length, head type, and drive type. An example is a wood screw, which is characterized by its wide thread and tapered head tip for screwing into wood. Another example is a machine screw, with a finer thread and a flat or round head for a secure hold in metal or plastic.
Conduct tests and quality control in
As a product development engineer, I would focus on a number of approaches that ensure both the reliability and performance of custom screws. This approach would mostly entail thorough testing and quality assurance. In this case, the necessary testing would include dimensional inspections, tensile strength testing and surface finish evaluation . These tests and evaluations would ensure that all the screws meet requirements and specifications, providing compliant and high-quality product . Additionally, this approach is bound to regulations and standards since the screws that would be used in aerospace and medicine would have to meet the standards set by ASME, ASTM or ISO certifications. As the representative of the customer, I would also ensure the implementation of these standards and regulations . As for the optimization of the production process, I would achieve greater efficiency by working with the manufacturer to reduce waste and optimizing manufacturing processes. The methods to optimize manufacturing processes include lean manufacturing, just-in-time production and continuous improvement. These methods help to reduce lead time and thus increase productivity while maintaining the standards and quality of the product. Since ASME, ASTM or ISO certifications dictate that the manufacturer needs to have a Quality Management System in place, it would also provide a basis for consistent and improving production of high-quality custom screws . Moreover, in order to keep up with the advancements in screw manufacturing, it would be necessary both to stay up-to-date with the research and development through regular meetings and conferences with the manufacturers and other professionals and to create working relationships with the same individuals to encourage collaboration and feedback . Therefore, I would ensure that the manufacturing of custom screws that I need would be consistent with the standards and requirements in place.
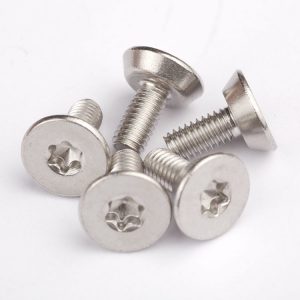
M4 Screws Custom Made
Catalog of Screw Types and Head Styles
Exploring Common Screw Types
Explore the different types of screws, including wood screws, machine screws, self-tapping screws, and drywall screws, used in a variety of applications. Learn about each screw type’s specific use and unique thread design and point characteristics that can be used for specific materials and fastening purposes.
Understanding Thread Profiles
Learn about the different viable thread profiles, including coarse, fine, and self-tapping threads, and their central role in the design of screws. Understand the advantages offered by coarse threads for holding power in soft materials such as wood, fine threads for vibration resistance when applied to metals, and self-tapping threads for the absence of necessary predrilling by cutting its additional thread profiles in such materials as plastic and sheet metal.
Analyzing Head Styles
Understand and analyze different head styles applied to screws, focusing on flat, pan, oval, and round heads. Take note of the specific applications and screw features of each head style, including the flush finish of flat heads, the enlarged surface contact in pan heads, and the decorative appearance of round heads.
Examining Drive Types
Learn about fasteners’ different drive types, including Phillips, slotted, hex, Torx, and square drives, and consider their advantages. Understand that each drive type offers different attributes, such as torque transfer, resistance to stripping, cam-out, and ease of use, that can enhance their applicability for specific purposes. Specifically, familiarize oneself with the use of Phillips and slotted drives for general applications and the use of Torx drives for improved torque transmission and cam-out resistance.
Reviewing Materials and Finishes
Review and learn about the different materials from which screws are made, such as stainless steel, carbon steel, brass, and zinc-plated steel, and their respective finishes. Understand that the specific material and finish of a screw is defined by its unique properties, strength, and ability to withstand corrosion and meet the specific application needs. Therefore, learn how to choose the sheen and type of screw based on whether it will be used outside or inside and its specific purpose or aesthetic requirements.
Understanding Size and Length
Learn about the meaning and importance of the size and length of screws in their use and understand that this is defined by a number or gauge, such as 6 or 1/4”, referring to the screw shaft diameter. Also, become familiar with the difference in length measuring techniques from the tip to the head’s underside, varying with the material’s thickness.
Selecting the Right Screw for the Job
Understand that choosing the right screw for the job is essential and that it must be done identically or according to the application requirements. Check that the chosen screw is highly resistant to corrosion and load bearing and appropriate for the material used and that it incorporates the necessary head style. For applications featuring a high risk of tampering, this may be a special screw, such as security screws, tamper-proof screws, or threaded screws with unusual heads. If in doubt about choosing a screw, it is best to contact a production specialist or a screw supplier for guidance on the application and material requirements.
Match Screws to Industry Specific Needs
Identifying industry-specific requirements. Identify different industries, such as construction, automotive, aerospace, and electronics, which have unique demands on the strength, corrosion resistance, temperature tolerance, and other performance factors of screws.
Analyzing material compatibility. Analyze screw materials that could serve industry-specific applications, such as the preference for stainless steel in the marine industry due to high corrosion resistance. Similarly, titanium screws are used in the aerospace industry due to their light weight and high strength-to-weight ratio.
Understanding load-bearing requirements. Analyze the load-bearing requirements of different industries to ensure that screws can withstand the required weight and stress. For example, the screws that join parts in construction require strict compliance with load-bearing requirements to ensure the safety and stability of the structure.
Considering environmental factors. Consider different temperatures for screws exposed through various industry applications and chemicals. For example, screws used to install outdoor signage should not degrade in the sun, and they should not be affected by widely fluctuating summer and winter temperatures.
Selecting corrosion-resistant coatings. Select different types of corrosion-resistant coatings for the screws working in the unique demands of industries, such as galvanizing, zinc plating, and ceramic coating for the marine, automotive, and industrial industries. Perform necessary testing processes afterward.
Choosing specialty screws for different applications. Purchase highly specialized screws for different applications, such as metal-fabricated self-drilling screws, plastic-component thread-forming screws, and electronic-device captive screws.
Customizing screws for different requirements. Customize screws for different industries by working with manufacturers to choose the required size, length, thread pitch, and head style.
Testing screws for their performance and reliability. Test screws for different applications’ reliability through vibrations, temperature cycling, mechanical stresses, and other testing procedures. Finally, screws can be accepted or rejected according to common industry standards through third-party testing.
Establishing Quality Standards and Certifications
Defining quality parameters: Define quality parameters for screws, such as dimensional accuracy, material composition, mechanical properties, and surface finish. Compliance with these parameters ensures the screws meet the required standards and be safe, precise, and reliable in any application.
Adhering to industry standards: Make sure the screws manufacturing adheres to industry and application-specific standards and specifications, such as those provided by ASTM, SAE, and ANSI/ASME. By following these standards, the screw’s design, materials, manufacturing processes, and quality assurance mechanisms are reliable over time and in all applications.
Implementing quality management systems: Implement a quality management system to ensure and maintain systematization and traceability of the screws manufacturing processes. Systems such as ISO 9001 provide guidelines for manufacturing quality control, inspection, testing, and documentation, providing reliable instruments to fulfill customers’ requirements and comply with applicable regulations.
Obtaining certifications: Obtain certifications such as ISO 9001, IATF 16949, AS9100, or RoHS compliance to ensure the manufacturer meets customers’ requirements and regulation standards. Certifications are an important advantage for customers, as it guarantees that the manufacturer adheres to the industry’s standards and that its products meet the requirements.
Quality assurance testing: Conduct quality assurance testing to the screws to ensure they comply with the relevant specifications. These tests may include dimensional inspection, tensile strength, hardness, and surface finish tests, as well as corrosion resistance and physical dimensions test.
Statistical process control: Implement and use statistical process control techniques during the manufacturing phase. Tools to be used include control charts, the process capability analysis, and the Pareto analysis to monitor the processes performances, detect trends, deviations, and implementing corrective actions in time to achieve continuous improvement initiatives.
Training and education: Training and educate the staff involved in screws productions with information and practical applications related to quality standards. These training programs may include the discussion of quality control techniques, dimensions, inspection methods, and applications.
Supplier quality assurance: Implement supplier quality assurance in order to make sure the firms’ suppliers comply with the manufacturing specifications. A supplier quality audit and the implementation of a quality agreement between the two companies are highly effective in making certain that supply is consistent and that there is no non-conformance.
Corrective and preventive actions: Implement a corrective and preventive action plan in order to timely address non-conformities, deviations, and complaints. Immediate corrective actions, problem investigation and solution implementation, and the establishment of preventive actions are important to avoid any deviation recurrency.
Continuous improvement programs: Implement continuous improvement programs, and initiatives to keep innovation, efficiency, and quality excellence at the highest possible levels. Employee involvement and activity participation to improve and innovate new processes, and added-value products result in a greater customer service-.
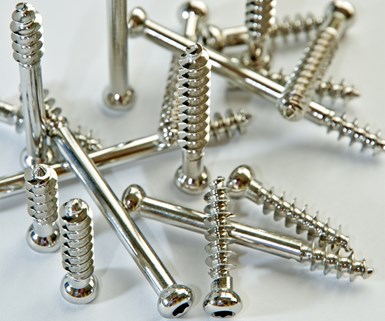
Medical Screw Solution Includes
Selecting the Right Manufacturer for Your Needs
Understanding Your Requirements
Identify your specific requirements for screw manufacturing, including quantity, size, material, and quality standards. Determine the application and performance criteria to be sure they are compatible with your intended use .
Researching Potential Manufacturers
Conduct thorough research to identify potential screw manufacturers who meet your limitations. Utilize online resources, industry directories, as well as referrals from colleagues. Create a list of manufacturers who are considered to be reputable.
Assessing Manufacturing Capabilities
Evaluate the manufacturing capabilities of each potential manufacturer , including equipment, technology, and expertise. Locate the manufacturer who uses advanced machinery and people experienced in producing the screws in your quantities .
Reviewing Quality Assurance
Review the quality assurance processes implemented by each manufacturer to ensure they work . Inquire about quality control and inspection procedures and look for ISO 9001 certification .
Requesting Samples and References
Require samples of screws produced by each manufacturer and check the fit . Obtain references from earlier clients and keep in touch with them to be sure everything will be as you expect .
Comparing Pricing and Lead Times
Compare pricing and lead times provided by each manufacturer and chose the manufacturer who has the most attractive conditions, in terms of practical value and the shortest period of time needed .
Visiting Facilities and Meeting Teams
Visit the facilities of the top contenders on the list and meet with the team, including an engineer or production manager, and a quality assurance team. Describe your requirements and expectations .
Negotiating Terms and Agreements
Negotiate terms and agreements, including price, delivery schedules, and quality guarantee . Make everything clear for each possible misunderstanding.
Establishing Communication Channels
Make sure you have a contact person with the manufacturer in case of any changes in your requirements or orders .
Monitoring Performance
Measure each manufacturer’s performance and rely on your gut instinct – if you did not like anything, do not congratulate yourself on finding a mistake in the system .
Building Long-Term Partnerships
Try to build long-term partnerships with the manufacturers who satisfy your needs. Such relationships assume ongoing communication, respect for each other, and a good product.