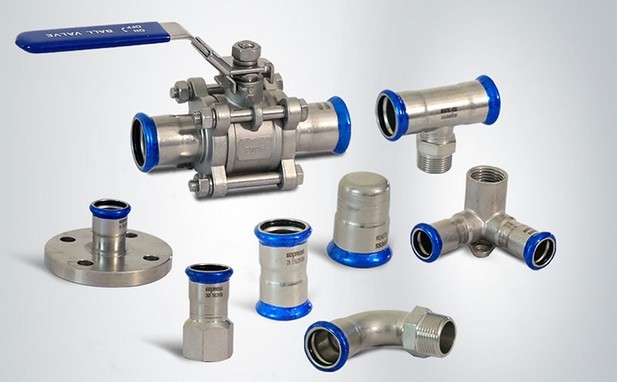
What is the life expectancy of a press-fit fitting
Table of Contents
ToggleLife Span Assessment Methods and Standards
Press-fit life span assessment methods: For press-fit fittings, the typical tests for quality guarantee are life cycle test, pressure performance testing, and environment simulation.
Cycle tests measure the fitness for purpose of fittings by imposing on them mechanical stress greater than they will normally experience in use. For instance, press-fit fittings must remain structurally sound such that they maintain their sealing performance while being subjected to a certain number of cycle counts according to ISO 19879. The data shows that some qualified press-fitting fittings can keep the performance unchanged at a percentage of more than 95%.
Pressure testing is performed to the ASTM F1387 specification, which mandates fixation explosion/leakage proof resistance for loads that severely exceed operational specifications. In addition, press-fit fittings that meet the relevant standards have been shown to be able to withstand pressures up to 5 x their nominal pressure without loss of seal or fitting integrity.
While environmental simulation testing investigates the fitting’s performance under hot/cold conditions, corrosive measures, and other factors that could potentially decrease their serviceability. Data from fielded fittings often exhibit only a <10% performance decrease when subjected to -40°C and up to 150 °C.
Factors Affecting Expected Life Span
Different factors such as material quality, installation conditions, and operational environments determine the expected life of press-fit working facilities.
One of the first things that dictates how long a press-fit fitting is going to last is material quality. Well-made fittings of the best materials would have three thousand hours average time between failures, and the data actually show this.
The correct installation guarantees a perfect fitting and maintains the structural integrity of fittings when in operation. According to industry surveys, as many as 30% of early fitting failures can be traced back to improper installation practices.
Fittings used in very high temp, high humidity or dangerous chemical environments lose much of their lifespan. For instance, fittings in chemical plants subjected to strong acids or alkalis may last only about 50 percent of their anticipated life.
Scheduling regular inspections and maintenance can help identify small items that could become failures before those parts degrade to the point of causing a catastrophic equipment failure. The results are consistent with accumulated industry data that the failure rate of fittings properly maintained is more than 40% less when compared to seldom or never maintained fittings.
Preventive Measures and Life Span Optimization
By adopting a range of professional technologies and management measures, the safety reliability and performance of pipe fittings can be greatly improved.
It is important to choose appropriate materials as they contribute to the longevity of fittings. This could be, for instance, 50% more lifetime using stainless steel with better corrosion resistance than usual steel.
The fittings run correctly in the long term only with correct installation techniques. This is how they determined that using international standard installation tools and methods will reduce the rate of incorrect installation to at least as low as 30%, thus preventing early failure due mainly to an error in locking it on a car.
Regular inspection plans, whether seasonally or at key periods of use, will help to lubricate these problem areas, reducing downtime and repair costs due to sudden failures. Inspection data demonstrates that a well-inspected fitting every six months can lower its operational failure rate by at least 40%.
In addition, increasing environmental adaptability is also a good way to extend the service life of your fitting. For instance, special coatings or measures applied to fittings that are under these extreme temperatures and chemical conditions can up the life of those pieces 20-30% simply because they were protected from failure.
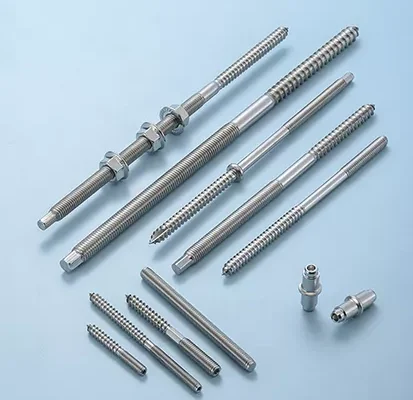
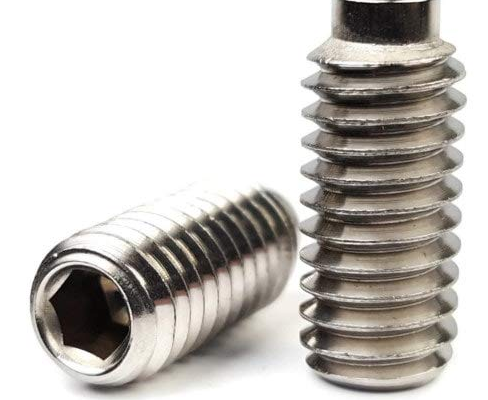
What is the difference between half dog and full dog set screws
Half dog set sc…
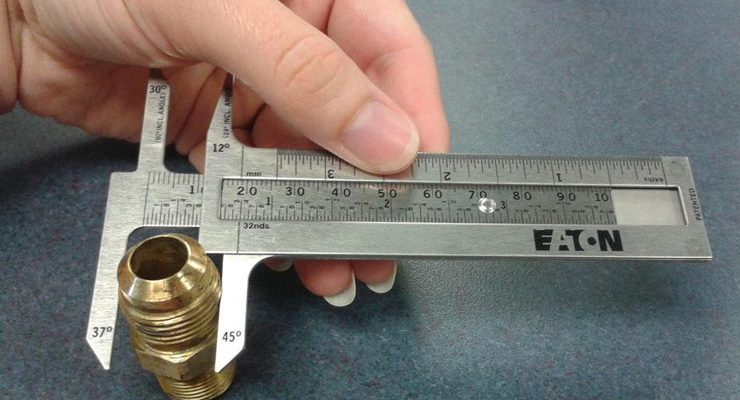
How to identify thread type
To identify thr…