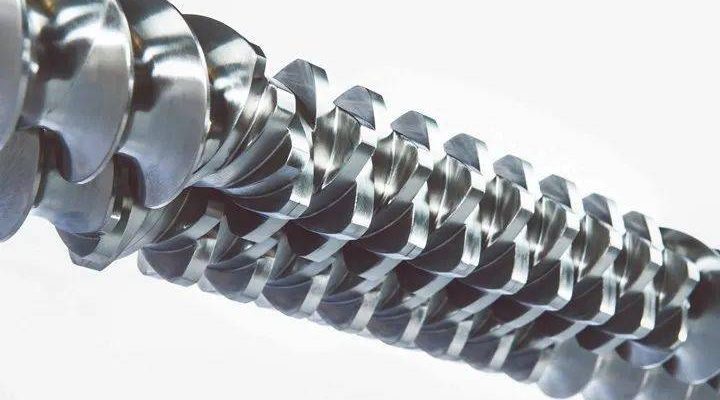
6 Common Mistakes In Twin-Screw Extruders
Proper warmup, feeding, temperature management, shutdown, maintenance, and material selection ensure efficient twin-screw extruder operation and product quality
Warmup Error
Warmup errors in twin-screw extruders are one of the most common problems leading to production down time and the waste of material. Errors in warmup often are consequences of incorrect settings or wrong preheating procedures. To avoid the errors and the unfavorable effects, the following steps should be taken:
Preheat the barrel and the screws properly: before starting the extrusion, the barrel and the screws of the extruder should be preheated to the specified temperature range. Typically, the preheat temperature for twin-screw extruder ranges from 150°C to 250°C depending on the material. The improper preheating results in degrading of the material and sticking that often causing blockages. Additionally, in case of wrong preheating, the output of the extrudate is variable in quality and quantity.
Temperature uniformity should be checked : the temperature inside the barrel should be controlled through the use of multiple thermocouples along the barrel between the screw and the barrel wall. The temperatures measured should be uniform along the barrel to avoid cold spots. The cold spots typically are due to uneven preheating and can decrease the quality of extrusion by melting and die swelling.
Gradual temperature increase : the temperature along the barrel should be increased gradually. This avoids thermal shock to the equipment and the material. Any rapid increase in temperature can result in decomposition of the material and mechanical stress on the screws and the barrel.
The heating elements should be monitored: the heat elements with the thermocouples should be checked and calibrated regularly. The parts should not be replace, if there is no evidence of a fault. Uneven heating of the barrel as a consequence of the failure of one or more heating elements is a common problem of warmup errors.
Use the right materials: the materials should be water and moisture free and correspond in the specification of the extruder. Different materials have different melting points and substances. Using incompatible material can result to clogging, poor extrusion properties or even health risks.
Follow the manufacturers guide: the manual of the manufacturer should be followed. It is based in general on the optimum equipment condition and typical warmup ok research and development.
Regular maintenance checks : as other technical equipment either should the screw extruder be regularly maintained depending on the through put rates, the material checks, and the type of extrusion. Worn parts for example can cause warmup errors.
Incorrect Feeding
Incorrect feeding in twin-screw extruders can result in a wide array of problems, including poor product quality, material waste, and equipment damage. Correct feeding usually involves making sure that the conveyed material is fed into the extruder in the correct parts, rate, and consistency. Below are the ways to avoid incorrect feeding:
Ensure material homogeneity. The fed material must be consistent in size, shape, and composition throughout. Inconsistencies cause the material to get clumped in the throat where it can block the flow or build up against the feeders, causing the flow rate to fluctuate. Sieves or screens can be installed at the hopper or screw tip to screen out larger particles and maintain the homogeneity of material.
Control feed rate. Either the rate is too fast or too flow, which promote a high possibility of incorrect feeding. For precise measurement, gravimetric or volumetric feeders are often used. Material overload due to too fast feeding not only means that the equipment capacity is exceeded but also causes the problem of over-filling. Specifically, if the rate of material to fill an extruder is too slow, the clogging of the screw feeder results. The material to feed into twin screw extruder must also match the conveying ability of the feeder.
Prevent material bridging. Material bridging occurs when the conveyed material forms a natural arch or bridge over the feed throats and refuses to fall. Setting agitators in the feeder’s hopper or the attached vibrators helps to take care of the problem especially when the material is irregular in shape or prone to clumping. Moisture and temperature of the material should also be checked to ensure that they fall within the appropriate cooling levels.
Proper feeding. The material and the mix must be consistent and uniform straight through. For materials that are difficult to blend, high shear continuous mixers are essential in order to maintain cohesion. The amount of material being fed should also be precise and should be within the proper filling levels. To do it, a feeder should also have a live hopper, and minimum wear and tear restrictions. All parts of a feeder–specially the screw and the hopper–must be properly aligned. A live bottom hopper should be used in challenging applications.
Poor Temperature Management
Twin-screw extruders’ poor temperature management inevitably leads to numerous issues, such as product defects, equipment damages, and lower efficiency. In particular, the stability of operating processes and the accuracy of manufacturing require a stable and controlled temperature. The following are the main ways of dealing with and avoiding poor temperature management:
Accurate temperature profiling: Develop a detailed temperature profile for the whole process of conducting extrusion. The profile will specify particular temperature settings for individual zones of the barrel and screws. Generally, for plastic materials, temperatures should be maintained between 180 to 260 °C, but they depend on the specific material processed.
High-quality thermocouples: Make sure that thermocouples are of high quality and make sure that they are put into the extruder at the right places. The latter is necessary for making the process of temperature measurement as accurate as possible. No overshooting can occur during poor temperature management if the thermocouples are put where they should be.
Regular calibration: Regularly check and calibrate all temperature control instruments. At least once a month, have the controllers calibrated and compare and label them according to the user manual. Poor temperature management is often caused by the fact that the instruments give incorrect data, and this can be avoided by regular calibration.
Use automated temperature control: Utilize automated systems of temperature control that can monitor the sensors and then adjust the heating and cooling in real time. This makes the temperature maintained constantly and any deviations compensated instantaneously.
Monitor cooling system: Do not underestimate the importance of cooling and focus on maintenance as much as on heating. Make sure that all the cooling outputs are free of dirt and contamination and that the cooling systems work properly.
Adapt materials and coatings: Finally, focus on the design and the materials to minimize problems. The barrel and the screws shall be made of materials that ensure best thermal conductivity. Use any form of coating or any other modern solution for increasing the speed and efficiency with which the extruder heats up..
Improper Shutdown Procedures
Improper shutdown of twin-screw extruders can result in equipment damage, material residue, and increased maintenance costs. Thus, the correct procedure helps to sustain the equipment and provide continued production quality. Here is how to avoid the most common shutdown errors:
Gradually reduce temperature: Lower the barrel and screws’ temperature slowly to avoid thermal shock. For instance, decrease the temperature by 10°C, reaching 100°C at the end. Quick cooling may result in solidification of the material within the machine, causing clogging and damage.
Purge the extruder: Purge the extruder with a proper purging compound or the subsequent material. It is crucial to eliminate any residue left within the barrel and screws. Keep the speed low, ensuring that all the material is purged. Subsequently, there is no degradation or contamination in the following batch.
Stop the feeder: Last but not least, close the feeder after completing the purging. Avoid feeding the equipment during shutdown. The process aims at letting the screw purge leftover material from the feed throat. If not removed, this material may also solidify and cause issues.
Run the screws: keep the screws running at low speeds for 1 to 2 minutes after turning off the feeder to avoid material hardening within the extruder. Stop the speed at around 10-20 RPM to ensure continued movement, low loading, and limited wear.
Clean the barrel and screws: once the machine is completely cooled, clean the barrel and screws if necessary. Follow all the relevant procedures, avoiding any damage, and prevent future contamination.
Check all the components: Inspect all parts of the machine, including the screws, barrel, and die after the cleaning process. If the screws need replacement , prepare them before the next production run.
Turn off the auxiliary equipment: Once the extruder is completely finished and clean, shut down the feeder, heaters, cooling units and all other peripherals.
Neglect Maintenance
Twin-screw extruders are essential tools for manufacturing numerous food and non-food materials. Unfortunately, neglecting their maintenance may cause a variety of operational errors, potentially leading to decreased efficiency, defective products, and increased costs associated with repairs and replacements. Thus, regular maintenance is crucial for promoting the optimal performance and extended life of the extruder. The following practices are critical in achieving that goal and avoiding the most common errors:
Regular Inspection Schedule: A detailed schedule should be created to allow checking all components of the extruder regularly. The screws, barrels, and die heads should be checked for wear, damage, and excessive residue build-up. At least one comprehensive inspection should be conducted every month.
Lubrication: All moving parts should be adequately lubricated to prevent their wear. The use of approved high-quality lubricants and adherence to the manufacturer’s recommendations for lubrication frequency and amount are crucial. The lubrication levels should be regularly inspected, and all bearings and gears should be sufficiently lubricated.
Extruder Should Be Cleaned Thoroughly: After each production run, the extruder should be cleaned, ensuring that no material is left behind. Appropriate cleaning tools and chemical solvents should be used to guarantee no material build-up that may cause contamination or potentially affect any next batch.
Monitor Wear Parts: The screws, barrels, and seals are the usual wear parts and should be closely monitored. They should be replaced as soon as they become excessively worn to avoid further damage and decreased efficiency. A stock of such spare parts that are particularly critical should be maintained to reduce downtime when a replacement becomes critical.
Check Heating and Cooling Systems: Heating elements, thermocouples, and cooling systems should be checked to ensure their proper operation. The temperature control systems should be frequently calibrated, cooling channels may become blocked and should be inspected. Proper heating and cooling are critical for ensuring consistent product quality.
Alignment and Calibration: The alignment of screws and other key parts should be checked regularly. The calibration of the extruder should be checked to ensure that all settings are accurate and working correctly. Misalignment increases wear and potentially undermines product quality.
Software Updates: The control software of the extruder should be updated. All updates from the manufacturer should be installed to improve performance and correct known mistakes.
Training for Operators: The operators should be educated about maintenance requirements and the importance of regular maintenance. Periodic training sessions should be held to ensure that staff is familiar with the most recent techniques and safety practices.
Use Incorrect Materials
Utilizing wrong materials in twin screw extruder reduces the quality of the product produced, causes damage to products, and make the production process ineffective. Use the proper materials to ensure optimal performance and quality. These are the most common errors in selecting materials and their solutions.
Understand the material characteristics
Before using any material, you need to understand its characteristics. Understand if it’s melting point, viscosity, thermal stability, and compatibilities with the extruder component. The melting point of the material cannot be too high for the melting rate of the extrudes. Too high points cause incomplete melting and clog the extruder. Incompatible materials lead to corrosion of materials reducing the lifespan of extruder parts.
Match the material to the application
Materials used in the extruder must be compatible with the food grade and industrial standards regulations. Medical grade tubes must be extruded with a medical FDA approved polymers. There must be a continuous change in the properties pushed down the production channel. The products must possess the specified characteristics.
Do not contaminate the materials
Ensure materials used are free from contaminants. Another cause of contamination is unchecked impurities interacting with the materials. They grey materials and reduce their mechanical properties. They also lead to the formation of dots and reduces the color intensity of the finally produced outcome.
Material pre-treatment for a process
Some materials must be treated before the process of extruder. They include drying of the materials before processing to remove the moistures of the materials. For example, nylon must be dried before the percentage moistures of the materials drop to 0.2% or less to ensure that processing is successful.
Consulting with the suppliers
Work with the suppliers too if you have selected the materials. Some materials cause high losses during the feeding stage, for example, westrim, technologies, Klomark, and kamoetil. Get the technical sheets of the materials before commencing operations on it.