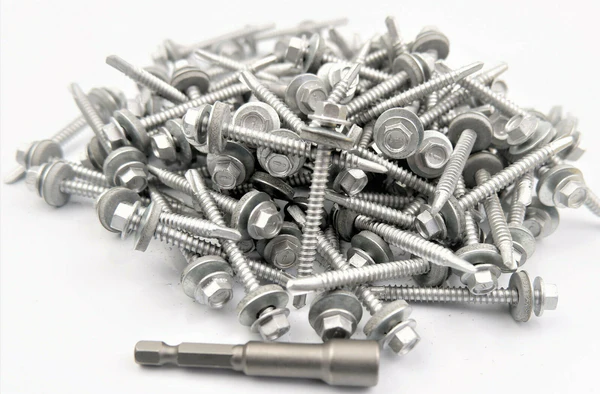
How to ensure quality in custom bolts
Specify material grades, request ISO 9001 certification, conduct rigorous tests, and perform regular audits to ensure the quality of custom bolts.
Table of Contents
ToggleSize and Grade: The Crucial Pair
One of the foremost things to understand about custom bolts and the quality of their manufacture is the very delicate relationship between size and grade of the bolt. While most custom bolts will run between 1/4 inch to two inches in diameter and from one to 24 inches in length, selecting the correct size for the product is not simply a matter of fitting it to the hole. Instead, it will significantly influence the performance of the bolt under load, its resistance to shearing and tension, and its resistance to any form of weathering or other deforming action.
Material Selection: The Foundation of Quality
Part and parcel of the issue of the loads a bolt will have to resist is the choice of material for the bolt, which will inevitably influence the bolt’s performance characteristics. For example, the high tensile strength of alloy steel makes it one of the most popular materials for construction and automotive bolts. However, in a marine application, it is likely important to emphasize corrosion resistance, which stainless steel provides. In both uses, the materials must meet the correct ASTM specifications to ensure they are capable of handling the correct loads.
Manufacturing Precision: Ensuring Exactness
Perfect precision in the manufacture of parts should be understood as mere baseline common sense. It is simply necessary for bolts to meet the exact tolerances defined in engineering blueprints. In addition to the use of the most advanced manufacturing techniques like CNC machining, the supply chain can also provide specially made tools like Davenport inserts for the purpose. This ensures that no matter the procedure used, each bolt is uniform in quality and easy to fit with the component it is designed to connect or hold. This include, among other things, avoiding any sharp edges that could produce additional points of stress.
Heat Treatment Processes: Enhancing Performance
Finally, it cannot be denied that the use of heat to modify the mechanical properties of bolts has become an essential aspect of bolt manufacture. Heat treatment can greatly increase the strength, hardness, and ductility of steel alloys, such as an increase in hardness to 32 on the Rockwel scale for a bolt untreated by heat. The key to proper heat treatment is, of course, to adhere tightly to the defined heating capacities and cooling patterns to avoid creating structural flaws in the bolt.
Quality Control Testing: The Assurance Step
Undoubtedly, volume testing of produced bolts is a key part of the manufacturing process. However, the intention of this testing is not only to sell bolts that meet the appropriate standards but also to provide an accurate snapshot of production quality. The use of a tensile test, proof load test, Charpy impact test, and other similar processes serve to ensure that each bolt produced can meet or exceed the loadings it is designed for. A comprehensive record-keeping system will provide an accurate record of which bolts were tested and the results, which can provide important follow-ups for quality assurance.
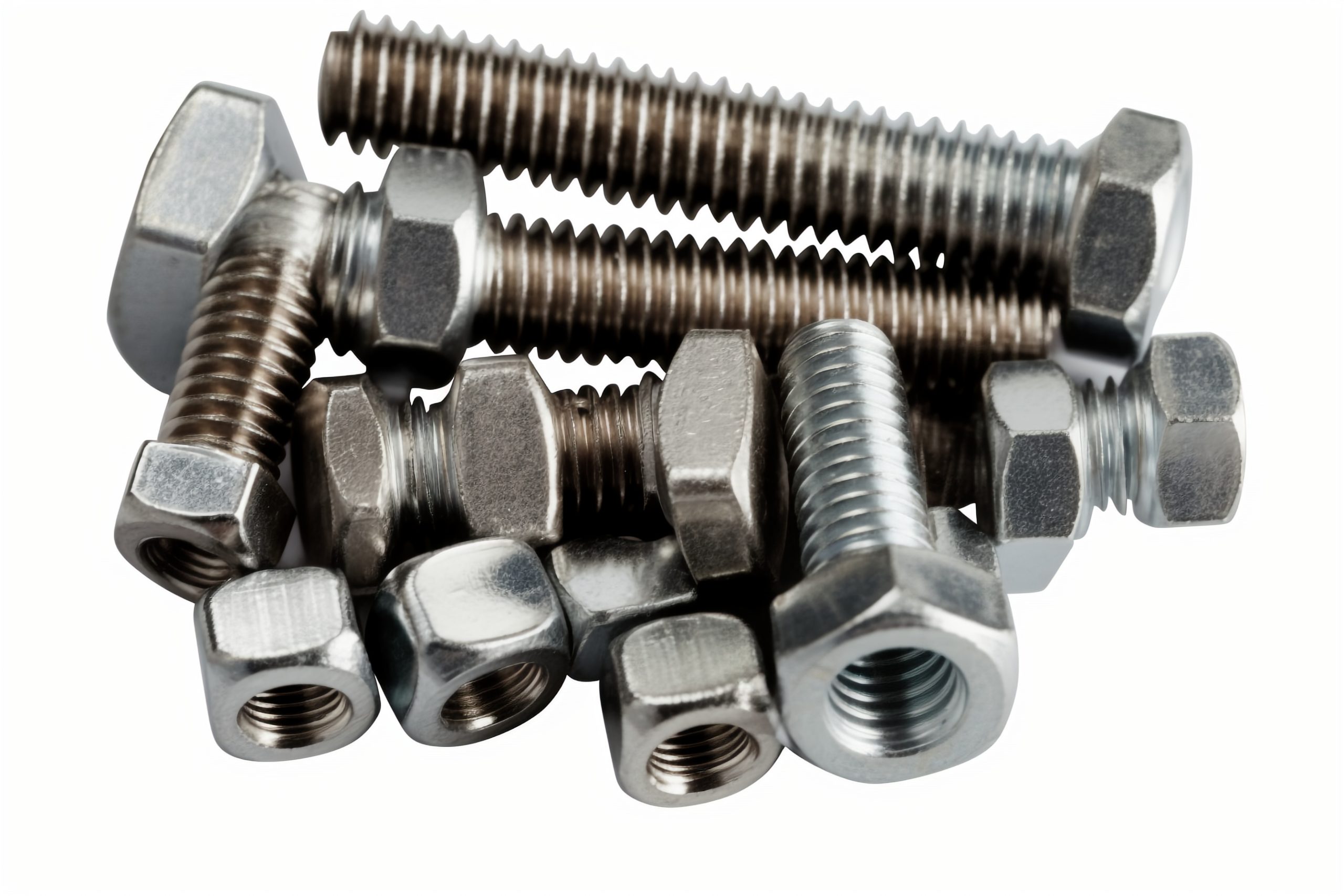
banner1
Quality of Material and Coating Benefits
Choosing the right materials for custom bolts is essential for them performing as designed under the same load and environmental conditions expected. High-quality materials such as ASTM A354 Grade BD or AISI 4140 feature enhanced durability and strength characteristics. Their yield strength can reach over 140,000 psi and the material ensures that the bolt won’t fail under any loads expected.
Advanced Coatings: Enhancing Durability and Performance
Bolt coating is not something that is done only to prevent the rust on their service; it also enhances the bolt’s performance and longevity. Zinc plated bolts are some of the most common ones, thanks to the fact that steel is always protected from the oxidizing environment and affordability. For more severe conditions, cadmium or PTFE coatings are considered. While the maximum temperature for working with cadmium is 500 °F, the PTFE reduces the friction during the assemble, making it easier, and can last even longer.
The Impact of Proper Coating
Proper coating can save the bolt’s lifespan but also make it more adaptable to different environments. For example, galvanized bolts will be perfect for any outdoor construction, thanks to the increased resistance to weathering. Each coating process follows a strict protocol of cleaning, bathing the bolts in the desired material, and curing, which may involve the heating of the bolts to ensure even treatment. In summary, the use of high-quality materials and testing the coating in high tech industries assures that every bolt will perform as planned, no matter the conditions; such detailed and qualitative production methods make the bolt and the manufacturers trustworthy and reliable.
Range of Custom Fastener Options
Diversity of custom fasteners is overwhelming; its range can be ordered to cater for every specific load, environment, or installation specification. Availability of specific options for every detail: length, diameter, thread size and style
Bolts can be ordered starting at 1/8 inch diameter and ranging to over 4 inches. Length can also be personalized; industrial length can be 100 inches and more
Custom thread designs
The design and thread pitch can be matched perfectly to fastener’s optimal grip requirements; can be made to withstand load and physical task
Coarse threads are used in construction because they resist stripping and are easier to handle. Fine threads are usually more applicable to infrastructure or automotive assembly
Specialty heads
The type of head can affect its usage and will mandate another set of tools. Bolt head options: hex for easy wrench access, Torx for better torque sustainability, low profile where the style is too cramped. Every design feature can find its specific use
Custom fasteners are not just an item; a special piece that is created by precise design and present on the market can seriously upgrade the quality of any item it is used for. Attention should be paid not just to the price but to special properties that it can be made to order. It is crucial to choose the right fastener by working through each custom detail and insisting on a consultation with an engineer.
Quality and Timeliness
In order to deliver custom bolts on time and at the required level of quality, it is necessary to have a properly designed operational framework. Product companies have to be equipped with a relatively strong quality control system and provide a safe and quickly produced product. It is extremely important to preserve a high level of quality at all stages and provide a flawless and precise procedure from the order coming to the final delivery.
Production Optimization as the Key to Timely Delivery
The most important precondition for delivering custom bolts as soon as possible is the strong positions of production. With the assistance of automated equipment and planning software, it is possible to ensure the shortest term of the production process. With the sufficient application of the JIT production model, the company avoids the need to store large amounts of goods and producing too many goods without the order being placed. This means that companies produce goods only with the respect to the customer’s orders, and this allows having the shortest time from the order coming to the delivery.
QC System: a Prerequisite for Reliable Result
Quality control is a center point in terms of ensuring the regular manufacturing of custom bolts. Each batch of products passes severe testing procedures, including dimensions check, quality of material check, and evaluation of behavior and characteristics at the simulated operating conditions. Taking into account that products are ordered by tens and hundreds, it is important to have a statistically modeled QC system that is able to guarantee the quality of goods at every production stage.
Incorporating the Customer Feedback into the Production Procedure
One of the design points that enable these bolts to be that good and meet the customers’ requirements is not only the well-functioning quality control systems. However, everyday production as an art nurtures from the samples and ideas received from the customers. This allows having a strong connection with them in terms of producing a perfect product that follows the customers’ demands in every single bit and adjusts to the changing trend patterns. Additionally, the feedback from the customers can help improve the manufacturing process and provide goods that are not stereotypical. If the described practices are followed by the companies, the timely cust of good delivery is going to be secured. Most companies that adhere to these delivery principles exceed these standards and deliver goods even ahead of the deadlines.
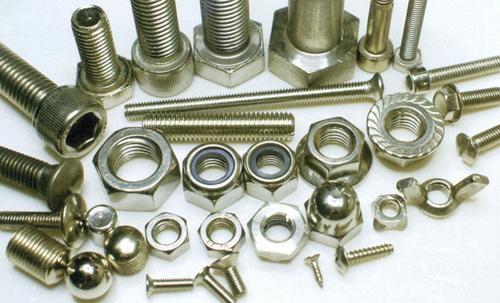
APL Bolts and Nuts
Implementing Quality Assurance Practices
Quality assurance in custom bolt manufacturing is not just another procedure; it is a conscious and ongoing effort to observe the standards that make products reliable and ensure that it’s possible to earn your customer’s trust. Thus, this process needs to make use of elaborate and detailed protocols to cover every part of production, extending from the selection of work materials, to the conducting of final testing.
The use of rigid testing protocols
The importance of testing in the context of bolt manufacturing does not need to be explained. Mechanical testing includes tensile testing, within which the frozen bolt is pulled from both ends, making it possible to determine the boss’s loading capacity, and hardness testing, within which Brinell or Rockwell scales are utilised for the purpose . For precise applications, it’s also a good approach to resort to ultrasonic testing, as it allows identifying the internal defaults within bolts, without actually causing damage.
Supervising the Qualifications and Compliance With Standards
There is a range of mandatory standards that make it possible to conduct proper testing and intense supervision: by complying with the ISO 9001 norm, the company states that its products have consistent quality. In the meantime, compounds and the products produced need to comply with relevant ASTM regulations. The compliance is to be observed on the level of recruiting specialists who comprise the QA team, and the standards are expected to follow by virtue of undergoing regular training and workshops.
All in all, it’s possible to state that by combining these practices and presenting a high-quality product, a bolt manufacturer also works a long way towards his establishing as a trustworthy provider of high-strength fastening agents.
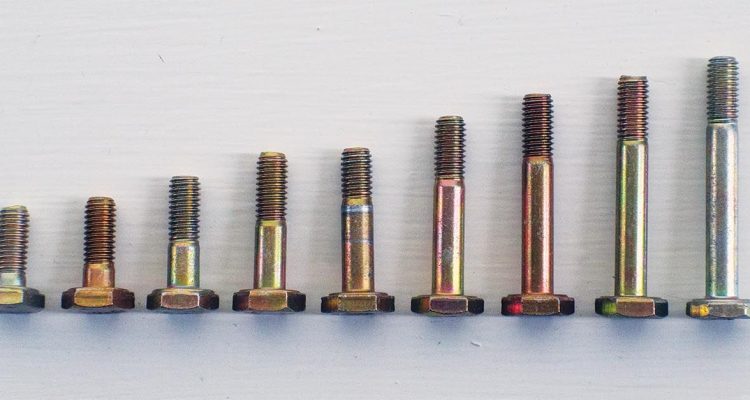
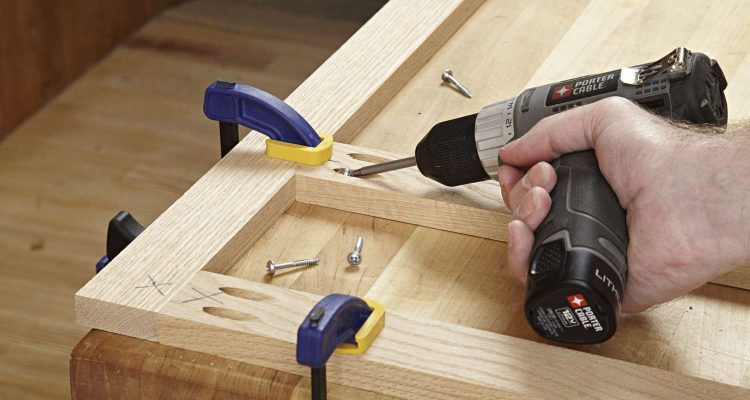
5 Common Mistakes With Pocket Screws
Common mistakes…
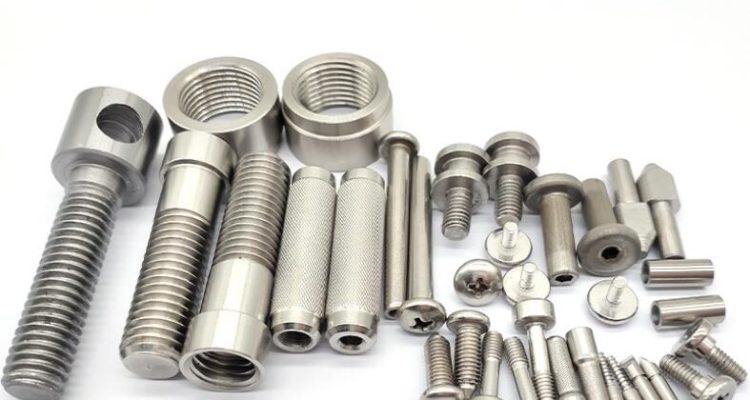
How to ensure quality when choosing a custom fastener provider
Ensure provider…